Aerospace Hose Assemblies: What They Are and Why They Matter
In the aerospace industry, safety and reliability are everything. Whether it’s a commercial jet or a military aircraft, every component must perform flawlessly especially the systems that handle fluid transfer under pressure. One key component often overlooked is the aerospace hose assembly.
These assemblies are responsible for safely moving fuel, oil, hydraulics, and air through complex systems while withstanding extreme temperatures, pressure changes, and constant motion. In this article, we’ll break down what aerospace hose assemblies are, where they’re used, and what components make them perform under tough conditions.
What Is an Aerospace Hose Assembly?
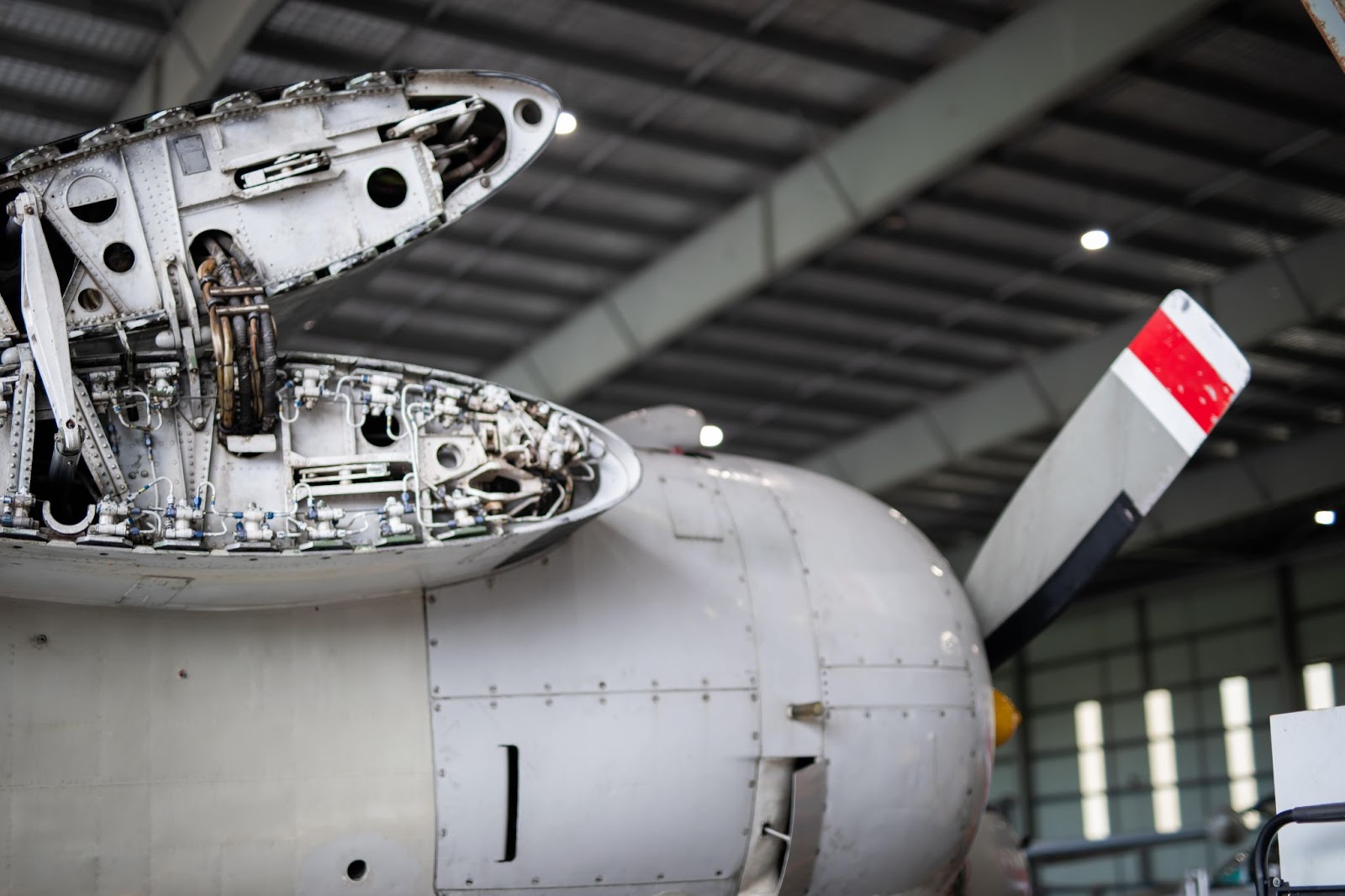
An aerospace hose assembly is a complete unit designed to transfer fluid or gas within an aircraft. It consists of:
- A flexible hose
- Fittings on one or both ends
- Optional layers of protection (such as insulation or abrasion-resistant covers)
Each hose assembly is tailored to meet the specific needs of the system it’s installed in whether that’s fuel delivery, hydraulic actuation, or environmental control.
Where Are These Assemblies Used?
Aerospace hose assemblies are found throughout an aircraft, including:
- Fuel systems – Carrying jet fuel from tanks to engines
- Hydraulic systems – Powering flaps, brakes, landing gear, and more
- Pneumatic systems – Managing cabin pressure and airflow
- Lubrication systems – Keeping engines and gearboxes running smoothly
- Cooling systems – Helping regulate temperatures in avionics and electronics
Each of these environments comes with unique challenges temperature extremes, vibration, corrosive fluids, and confined spaces. That’s why choosing the right hose, fitting, and protection is crucial.
Components That Make the Difference
Let’s take a closer look at the parts that make up a complete aerospace hose assembly.
1. The Hose Itself
The hose must be flexible, lightweight, and strong enough to handle the pressures of the system it serves. Aerospace hoses like these are typically made from materials like PTFE, rubber, or metal, and may include braided reinforcements for added durability.
2. End Fittings
Fittings connect the hose to the rest of the system. They must form a tight, leak-proof seal, even during intense vibration or pressure shifts. You’ll find a variety of fitting options here, from flared to flareless, depending on the application.
3. Protectants and Covers
In aerospace, hoses are often exposed to heat, abrasion, and environmental wear. That’s why many assemblies include hose protectants special sleeves or wraps designed to extend service life and maintain system performance.
4. Fully Built Hose Assemblies
Rather than assembling these parts on-site, many teams rely on pre-built hose assemblies that are tested and ready to install. This speeds up maintenance and ensures consistency across systems.
Aerospace Standards
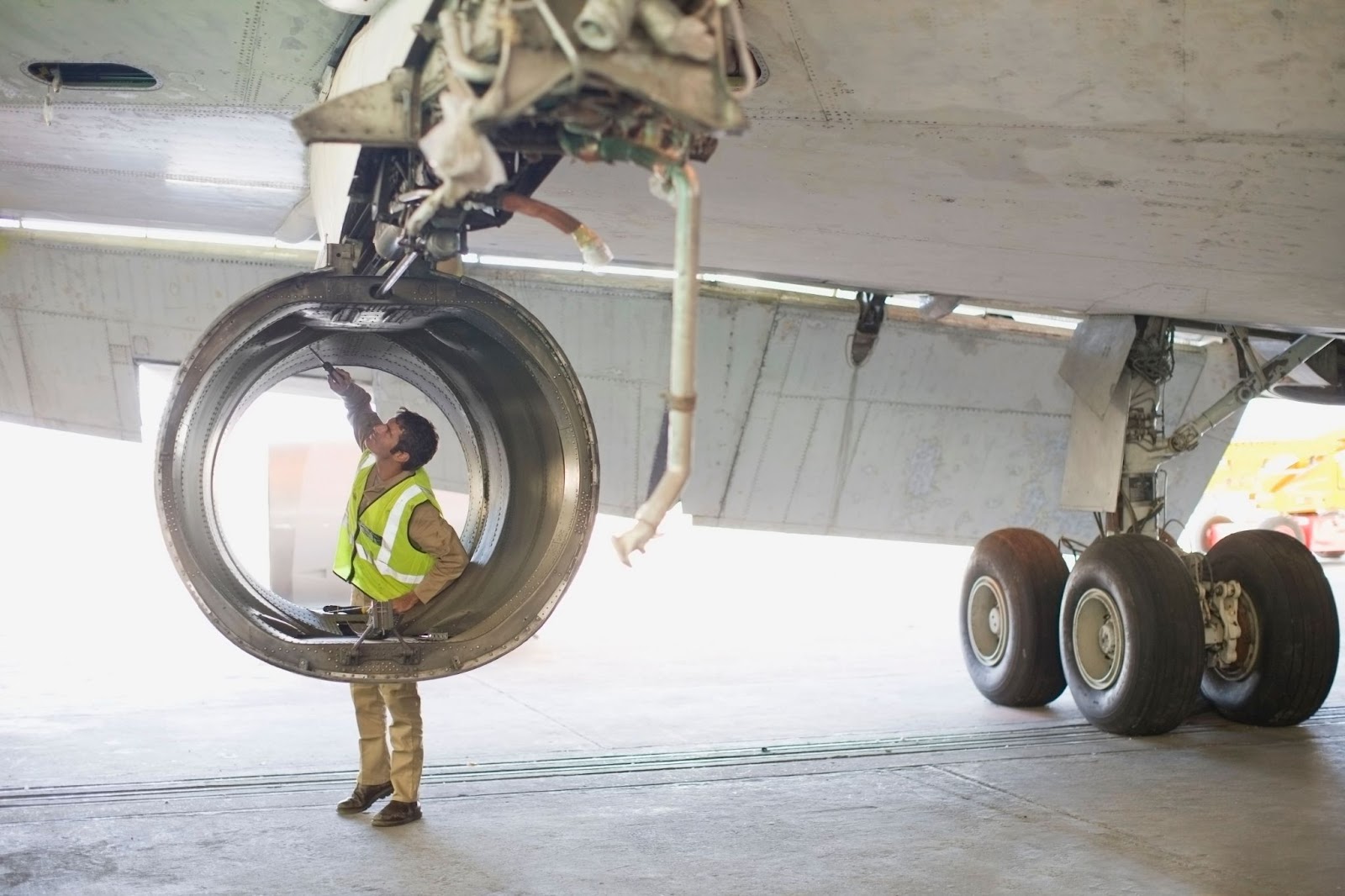
Not just any hose or fitting can be used in an aircraft. Components must meet strict industry and military specifications, such as:
- MIL-DTL-8795 for rubber hoses
- SAE AS1339 for high-temp PTFE hoses
- AS9100 for manufacturing quality standards
Every piece must perform under high pressure, survive rapid altitude changes, and resist chemicals like fuel and hydraulic oil.
Aerospace Hose Assembly Standards and Certifications
Reliability and compliance are vital in aerospace. Here are the major standards:
Standard | Organization | Description |
AS1339, AS1946 | SAE (Society of Automotive Engineers) | Aerospace hose specs and performance requirements |
MIL-DTL-877, 879, etc. | U.S. Military | Military-grade specifications for fuel/oil lines |
AS9100 | Aerospace Industry | Quality management system for aerospace manufacturers |
FAA PMA | Federal Aviation Admin. | Parts Manufacturing Approval for commercial use |
Suppliers and manufacturers must adhere strictly to these regulations to ensure airworthiness and flight safety.
Challenges in Design and Selection
Choosing the right hose assembly means thinking beyond just size and material. Engineers must also consider:
- Vibration and routing path
- Compatibility with fluids
- Flexibility for installation
- Burst pressure and temperature range
- Weight restrictions for aircraft efficiency
A small mismatch in any of these areas can lead to premature wear—or worse, system failure.
How to Choose the Right Hose Assembly Supplier
When sourcing aerospace hose assemblies, look for:
- AS9100 certification
- FAA PMA or MIL-spec approved products
- In-house testing and pressure validation
- On-time delivery and traceable documentation
- Proven track record in defense or commercial aviation
Types of Aerospace Hose Assemblies
Aerospace hoses vary by use-case and specifications. Below are some of the most common types:
Type | Application | Characteristics |
Teflon (PTFE) Hose | High-temp and chemical-resistant | Lightweight, high burst pressure, flexible |
Rubber Hose (Neoprene, Nitrile) | Low-pressure applications | Good vibration resistance, cost-effective |
Metal Hose (Stainless Steel) | High-pressure, high-heat areas | Excellent durability, fire resistance |
Composite Hose Assemblies | Multiple layer construction | Custom-built for specific weight and heat ratings |
Low-Permeation Fuel Hoses | Fuel containment systems | Designed to reduce vapor loss and fuel odor |
Final Thoughts
Aerospace hose assemblies might seem like minor components, but they’re essential to the safe and efficient operation of an aircraft. By combining the right hose material, fittings, and protective layers, these assemblies help keep systems running even under the toughest conditions.
Whether you’re working on a new aircraft build or maintaining an existing fleet, using well-designed, certified hose assemblies can make a significant difference in performance, safety, and downtime.
For a closer look at aerospace hoses, fittings, and full assemblies tailored for defense and aviation needs, you can explore this hydrasearch collection.